6 things to consider for a great UAV LiDAR integration
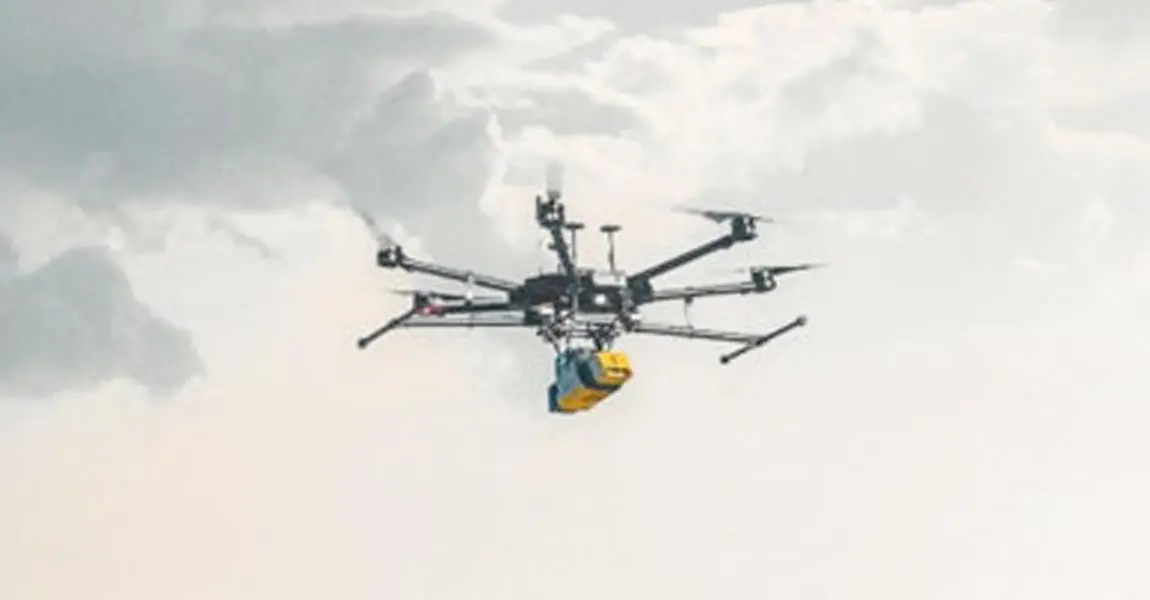
What should you consider for a successful UAV LiDAR integration?
UAV LiDAR integration is key to start a mapping business for safety reasons but not only (productivity, quality of deliverables…).
Here are 6 main things to consider:
1. UAV system endurance: 20+ minutes with a minimum 2kg payload is required. If not possible then you will lose productivity ;
2. LiDAR system ground clearance distance: 15 cm is minimum. Frame height above ground and legs lengths are to be considered. You need to take-off and safely. Even with great care and safe landing pad you can have objects (stones, branches) damaging the laser scanner ;
3. Mounting: The mounting is the critical part allowing LiDAR system attachment to the UAV. It should be resistant and light-weight. We’ve designed mounting brackets for this purpose:
– Standard 6-screws mount (to attach to the UAV frame)
– Quick and easy DJI M600 / M300 dedicated mount (<1min to attach)
– Quick and easy DJI M210 / M200 dedicated mount (<1min to attach)
4. LiDAR dimensions: The dimensions and global shape of the LiDAR system are relevant. A compact LiDAR system make integration easier. YellowScan LiDAR drawings and 3D models are available upon request to help integration;
5. Integration tests: Make your tests, step by step! We have mock-up LiDAR units at our facility. Using mock-up units definitely helps for integration tests and flights with less risks. Mock-up can be rented easily ;
6. Vibration isolations: We recommend vibration to be minimized to under 0.1g (on the straight lines), yet / up to 0.2g is fine. Vibrations may affect the quality of the data collection, break components from the LiDAR system or worse break the mounting and cause the fall of the LiDAR system. A mounting with dampeners is mandatory!
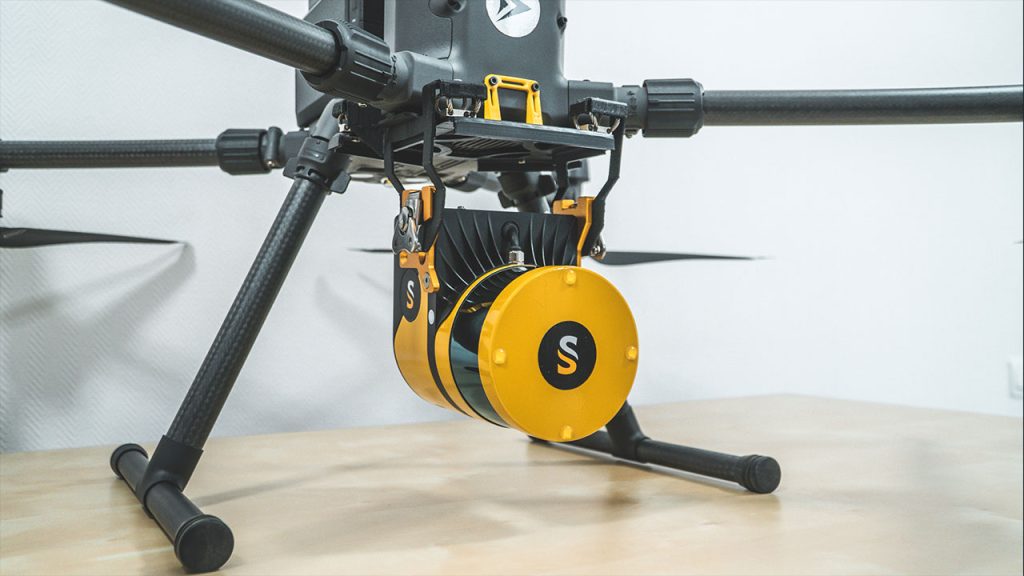
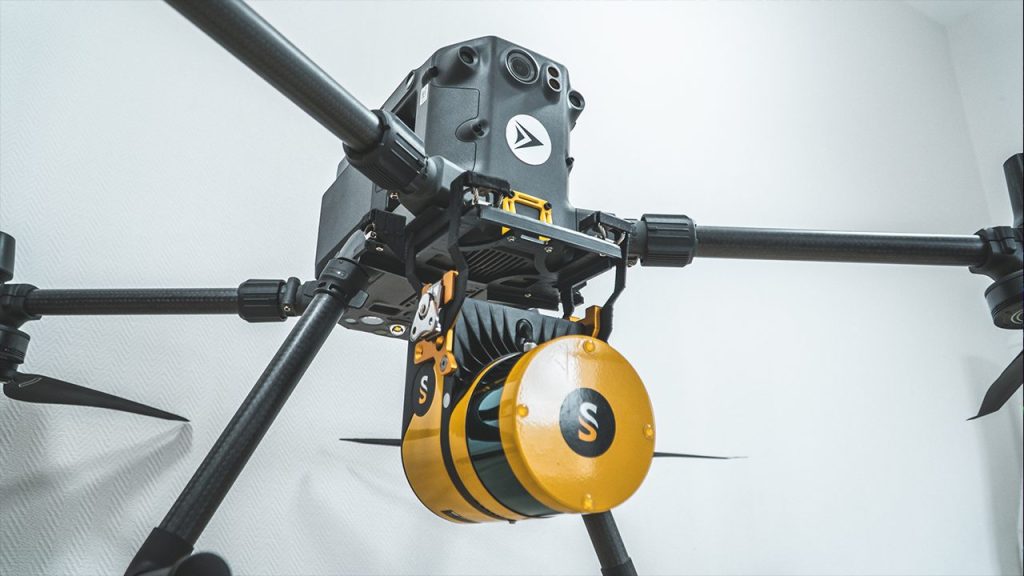
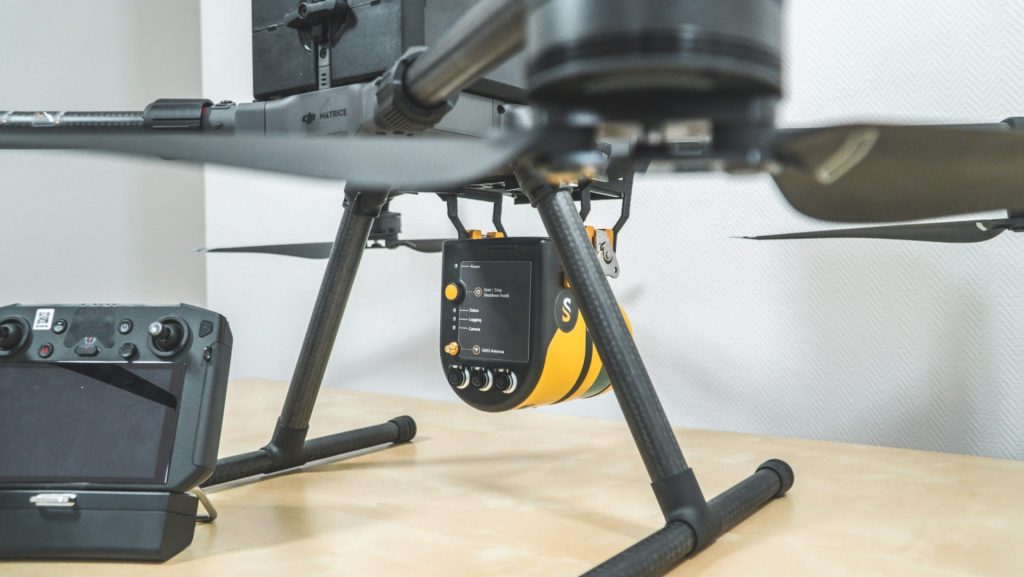
YellowScan Surveyor: example of UAV LiDAR mounted on a DJI M300.